3/8
Plant-Based Leaders | Danimer Scientific
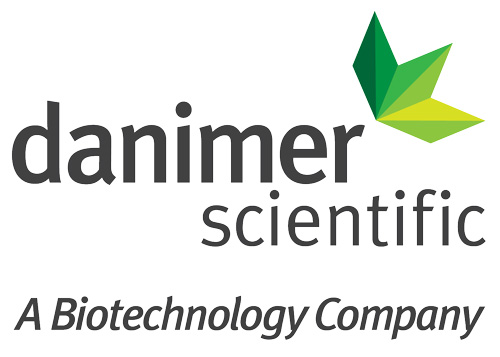
Danimer Scientific Delivers Adaptable Replacement for Traditional Plastics
Danimer Scientific spent over a decade developing biopolymer solutions at their research and development laboratories in Athens and Bainbridge, Georgia.
During those years the team earned numerous patents on its way to creating and improving a plant-based replacement for petroleum-based plastics which offers a remarkable array of properties to impress both the environmentally conscious and the business-minded.
Today, Danimer Scientific has a handful of locations across the U.S., including its production facility in rural Kentucky, the world’s first commercial scale production facility for their unique biopolymer known as Nodax® PHA, or Polyhydroxyalkanoate.
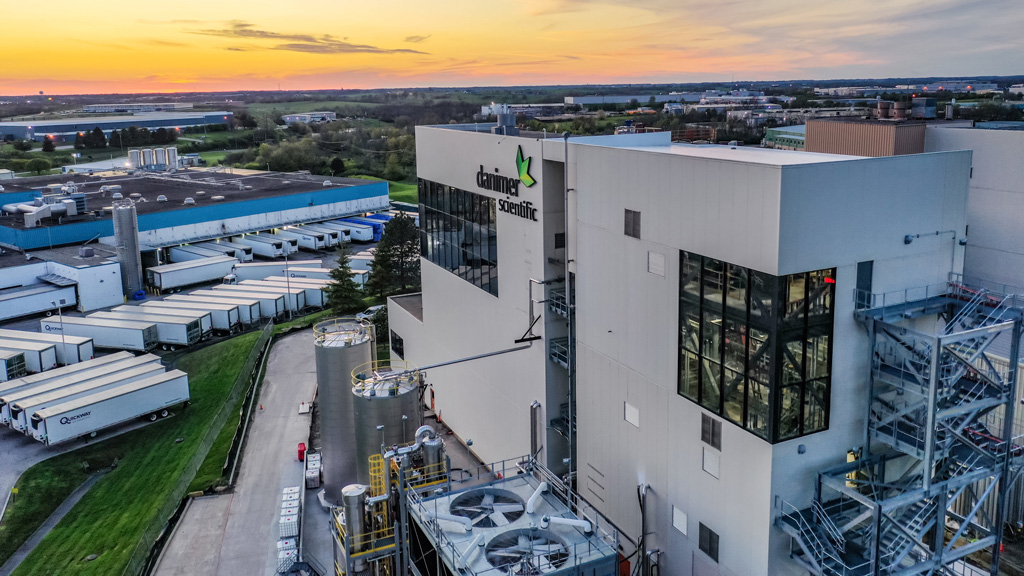
Replacing a range of fossil carbon plastics
PHA is a plant-based alternative to petroleum-based plastics able to serve as a renewable substitute across a broad spectrum of traditional products and applications – from molded plastics to adhesives to aqueous coating barriers.
It also offers tremendous benefits on the sustainability front.
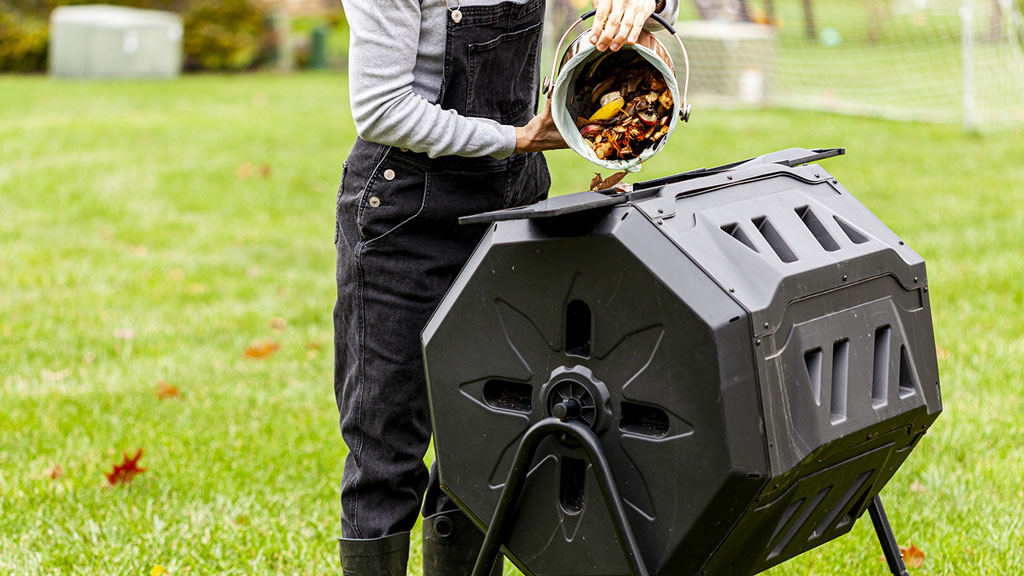
PHA degrades in both industrial composting facilities and home compost bins that consumers increasingly keep in their backyard.
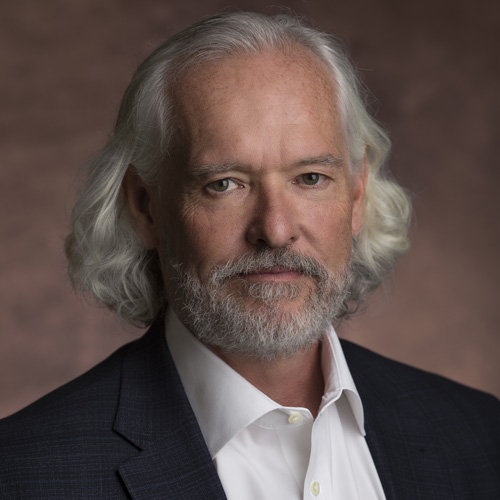
“PHA is certified to biodegrade not just in soil but also in marine and freshwater environments. It also degrades in both industrial composting facilities and home compost bins that consumers increasingly keep in their backyard,” said Stephen Croskrey, the company’s Chairman and CEO.
Petrochemical plastics persist in the environment for hundreds of years, shedding microplastics that today are found across our planet – from ocean bottoms to remote mountaintops.
“While there is always some variability based on local conditions, independent testing shows PHA will completely biodegrade in aerobic conditions in months, leaving behind only natural substances such as carbon dioxide, water, and biomass – and no microplastics,” explained Croskrey.
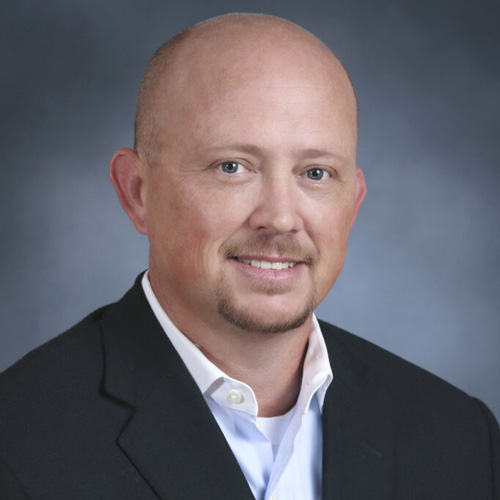
“We’ve put PHA through some of the most rigorous and widely accepted international standards and testing protocols for biodegradability in order to give our business customers and their consumers the peace of mind they deserve when they adopt PHA,” added Scott Tuten, the company’s Chief Marketing and Sustainability Officer.
Danimer Scientific’s facility uses proprietary microorganisms to produce PHA through a fermentation process, which is naturally occurring and commonly used to make foods and beverages we consume every day like breads and alcohol. The primary feedstock for PHA is renewable, naturally sourced canola oil, which can be grown through low-till and no-till farming. Much of Danimer Scientific’s canola feedstock is grown in the U.S. and Canada.
Customizable solutions
This fermentation process, guided by the company’s scientists and years of development, results in a range of products based on PHA that offer physical properties ranging from semi-rigid to highly flexible.
“PHA is unique because it is a customizable biopolymer. That means we can deliver an impressive array of goods with the same attributes as fossil-carbon plastics. PHA is already being used commercially for aqueous coatings, single-use service ware, and even dental floss applications,” said Croskrey.
Aqueous coatings are just one example of Danimer Scientific’s recent product innovations.
“These coatings have long been a serious challenge for the food service industry. They are used in products like disposable coffee cups and take-out food containers to ensure the liquids inside the package do not come into contact with the paper, which would cause leakage,” said Croskrey.
Such coatings have long been made from petroleum-based plastics (primarily polyethylene).
But as a result, compost facilities have refused to accept products coated with them, meaning such packaging ended up in landfills, or worse, leaked into the environment.
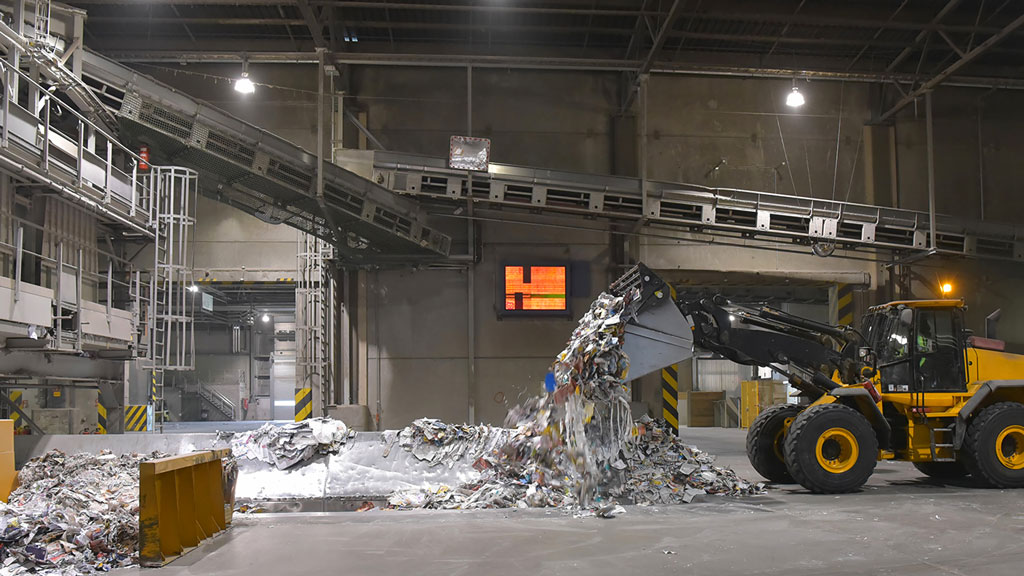
Our PHA based coatings are also repulpable, meaning they can be used in paper recycling centers as well. In both processes, we are helping close the loop on the circular economy.
“Our PHA based coatings are biodegradable, allowing them to safely enter compost facilities where they can become healthy soil. But the coatings are also repulpable, meaning they can be used in paper recycling centers as well. In both processes, we are helping close the loop on the circular economy,” said Croskrey.
And PHA offers much more than just aqueous barriers. This flexible biopolymer material, sometimes blended with other materials, such as PLA (a corn-derived biopolymer), can be crafted by company scientists into additives, extrusion coatings, adhesives, flexible film grades, injection molding, and thermoforming grades.
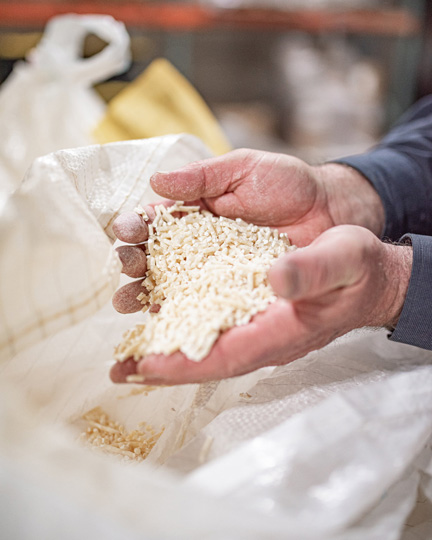
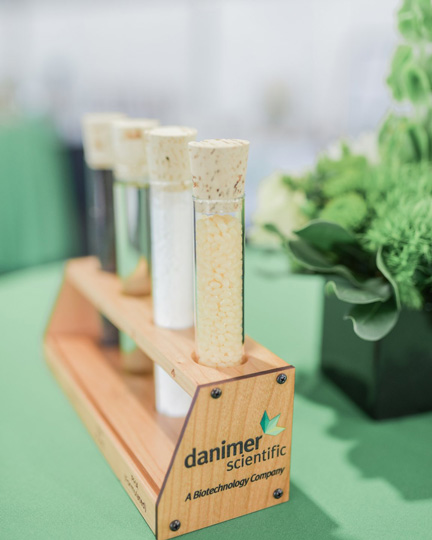
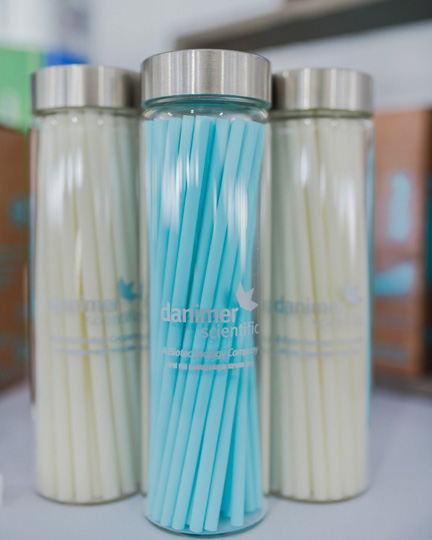
Within each of these product categories, the company’s scientists can work with clients to create specific formulations that meet customers’ exacting needs, whether a client is seeking strength, flexibility, durability, clarity, a specific melt point, moisture protection, or some mix of these or other attributes.
One of the most popular uses has been food service items often called single-use plastics (SUP), such as spoons, forks, straws, cups, and cup lids.
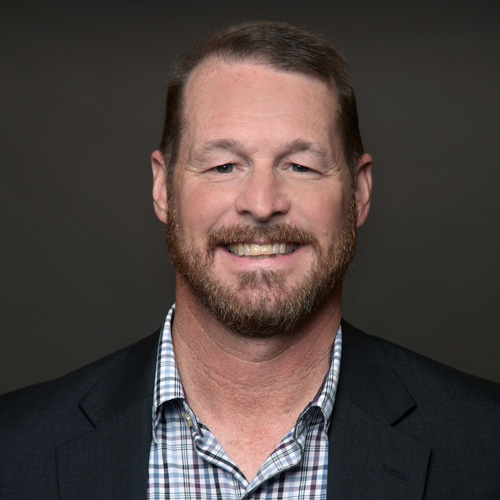
“The demand for safe, hygienic, and convenient food delivery methods will always be with us, and often that requires use of disposable products,” said Keith Edwards, the company’s Vice President of Business Development.
But sometimes consumers do not dispose of them properly, which leads to litter and consequently has resulted in bans of SUP products in some cities.
“No one wants to see these products leak into the environment,” said Edwards. “But rather than ban the single-use products that consumers need, we can offer a better solution to the food industry.”
Today, compostable and marine biodegradable straws based on Danimer’s Nodax PHA can be found at leading brands including Dunkin Donuts, Legal Seafood, Bonefish Grill, Tropical Smoothie and Starbucks.
Innovating with PepsiCo, Mars, and more
Among Danimer’s best-known clients and partners in research and development are Bacardi, PepsiCo, and Mars Wrigley – some of the world’s largest consumer packaged goods companies.
PepsiCo is a longstanding R&D partner, working closely with the Danimer Scientific team on compostable snack packaging innovation.
“Most consumers assume when they buy a bag of chips, the bag is just a bag,” said Croskrey. “In fact, it is a highly engineered product made up of nine to eleven individual layers and then fused together.”
That package has been optimized over decades for product protection, water vapor barrier, oxygen barrier, shelf stability, and other traits to ensure the chip quality meets consumer expectations, and the food product is protected throughout the supply chain.
“We’re working with PepsiCo to create a plant-based version that delivers on all of those necessary commercial traits and is still biodegradable,” said Croskrey.
It’s partnerships like these that have fueled Danimer Scientific’s growth, allowing it to become an economic engine in the communities where it operates.
A rural success story
Founded in 2004, in the rural community of Bainbridge, Georgia, the company has since invested over $600 million into PHA, creating hundreds of high-quality jobs in manufacturing and STEM-related fields.
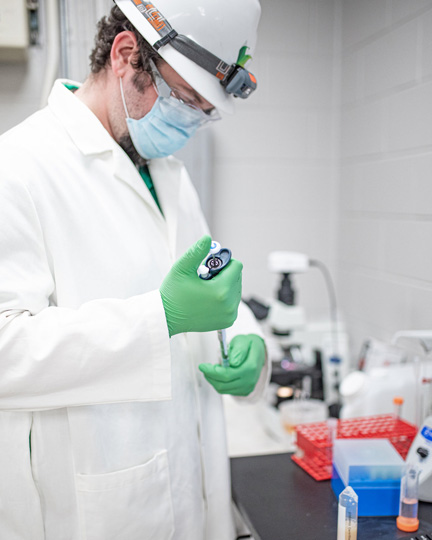
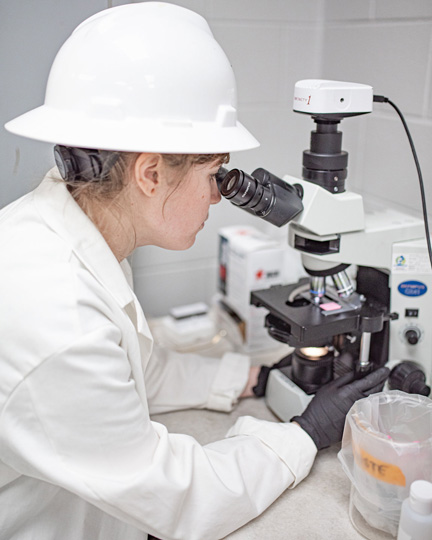
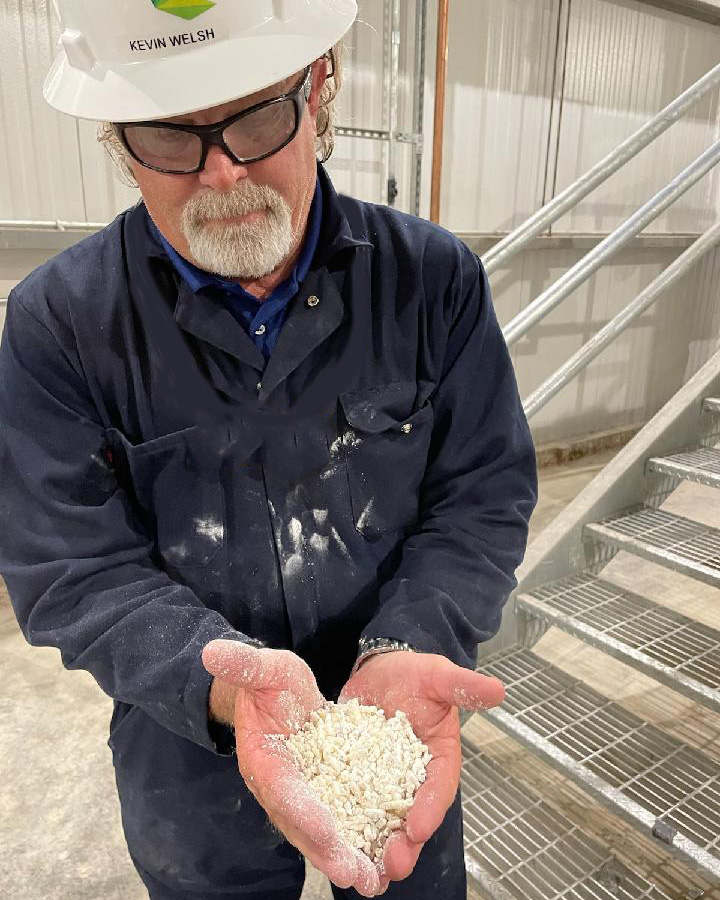
In 2018, Danimer Scientific purchased and retrofitted a shuttered fermentation facility in Winchester, Kentucky, another rural community. Today, Danimer employs 110 people in Kentucky and over 170 more across its other locations, including Georgia and upstate New York.
The Kentucky location is also a leading supporter of local agriculture, helping support farmers and working to create a co-op for growing and crushing seed oils, which can be grown on marginal land less suitable for other types of agriculture.
A role for government incentives
But plant-based products and the bioeconomy compete directly with the petrochemical industry which has a century-long head start and an enormous financial advantage – built in no small part from various government subsidies over that period.
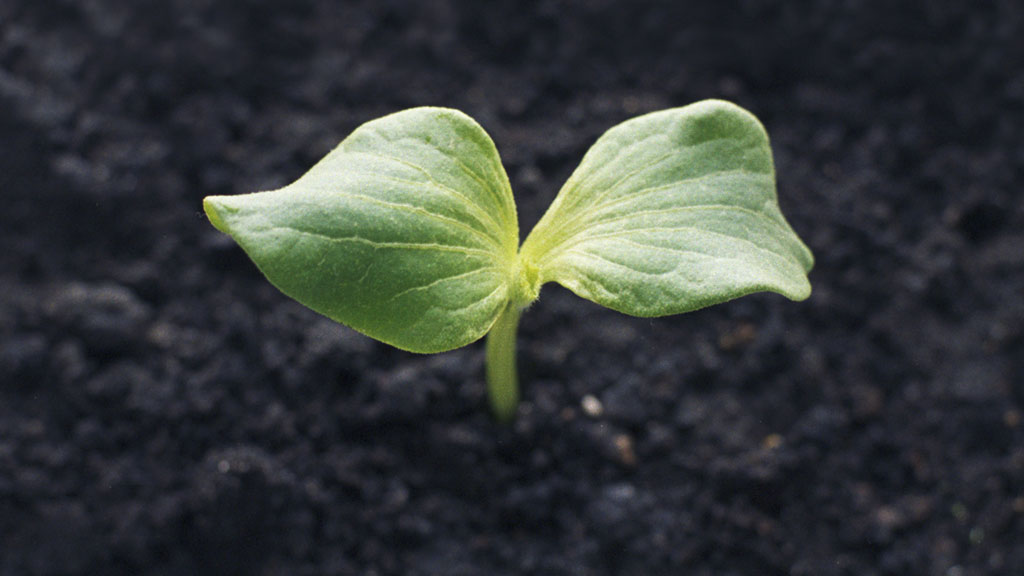
If our goal is to transition away from fossil carbon and toward a greener, circular bioeconomy, we need to build new technologies that compete with fossil fuels.
“If our goal is to transition away from fossil carbon and toward a greener, circular bioeconomy, we need to build new technologies that compete with fossil fuels. To be competitive, though, we must incentivize bioeconomic development,” said Croskrey.
“The fossil-plastics industry has huge advantages, from fully depreciated assets to years of optimization of manufacturing processes, while the emerging biobased polymer industry does not yet enjoy the same economic incentives as the biofuels industry,” noted Edwards.
Both renewable biofuels and renewable biopolymers draw from the same American agricultural feedstocks and aim to compete with the same fossil fuel behemoths. Recent government initiatives aim to address the gaps.
“The Biden Administration has recently announced government funding, grants, and loans that are becoming available to help give the biopolymer industry a jumpstart. That is a fantastic first step and it will play an essential role in incentivizing and supporting new technology and new innovations, like PHA biopolymers,” added Croskrey.
Federal guidance on waste management could improve the circular economy
Danimer Scientific points to another area where federal policy could make a similar pivot to boost the industry: waste management and end-of-life targets.
Petroleum-based plastics are a substantial portion of our nation’s solid waste, leaking into the environment, and filling up landfills. Those plastics are often enmeshed with valuable organic waste, which can and should be repurposed and recycled through composting.
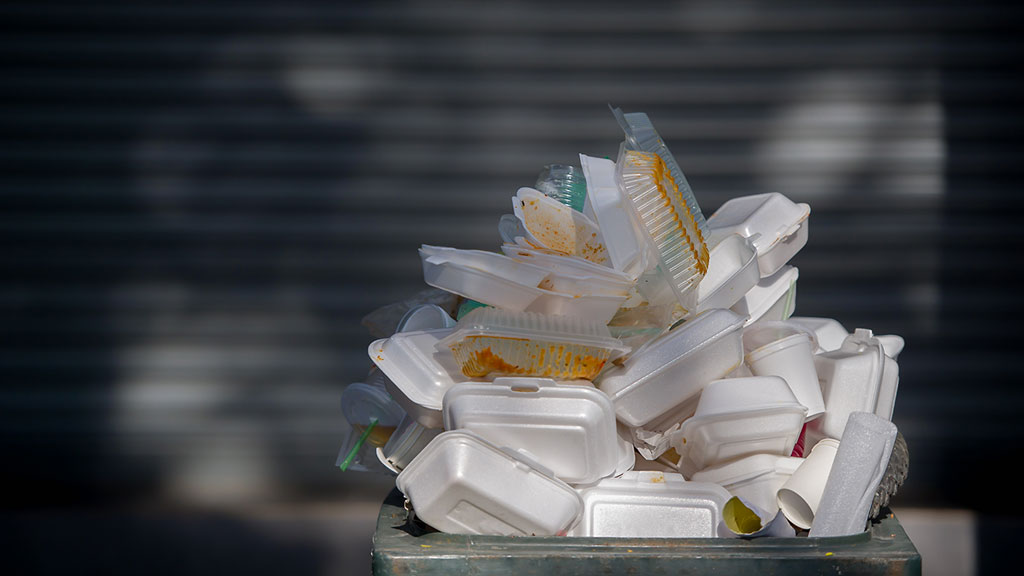
If you could replace food packaging with biopolymers, and then divert those products plus paper and food waste from landfills, it would have a significant and positive impact.
“If we want an effective circular economy, we have to deal efficiently with organic waste,” said Tuten. “If you could replace food packaging with biopolymers, and then divert those products plus paper and food waste from landfills, it would have a significant and positive impact.”
Today, a few states are leading the charge on waste stream management by deciding what can be accepted at various facilities.
But state level efforts are resulting in divergent standards.
“Brands need consistent guidelines so that they can create and deliver products that can enter the circular economy across the country. A national framework for policy making would greatly support this,” said Edwards, who works with groups like the Plant Based Products Council to drive policy.
After all, healthy compost is a path toward soil reclamation. It helps retain water and can reduce the need for fertilizers and pesticides.
To reach that goal, “we need similar organic waste management policies in every state,” Edwards added.
How the Plant Based Products Council (PBPC) drives federal policy
PBPC is helping to lead the industry forward on these and other issues.
“PBPC is one of the few organizations that’s really moving the needle for our industry – working in Washington to both promote and support the transition to a biobased economy,” said Edwards.
“That work is essential not only to the health of our industry, but the future health of our planet,” he added.
Join our growing group of plant-based leaders working toward a more sustainable economy. Learn more about the benefits of PBPC membership.